レイアウトをもとに金型を設計する。
1)ガイドポスト
精密微細金型では、ガイドポストの精度が重視される。
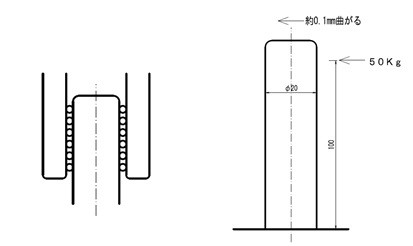
(1)ダイセットガイドポスト
ダイセットのガイドポストは、側圧に弱くプレス機にスラスト方向のガタがあった場合は金型破損の対策にはならない。手で持てないほどの大きな金型で型内ポストに誘導する目的で使用する。
※金型が手で持てる程度の大きさであればダイセットガイドポストは省略し小型化とする。
(2)ストリッパガイドピン
金型の精度を確保するために必須。
出来るだけ太い径で生産量が多い金型の場合は超硬製精密級(2μm精度)を採用する。
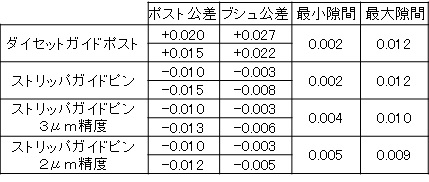
2)金型サイズ
金型事例
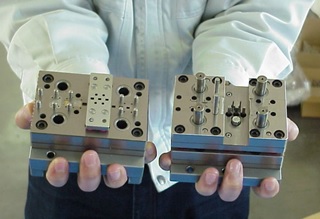
精密微細順送型は加工する製品が微細なので金型部品も微細となる
微細な金型部品は金型を組み立てる際に取り扱いで破損することがあるので、出来るだけ小さいサイズとする。
横から穴を抜いたり曲げる場合は、プレス機上下動を横に変換するカムとなる
カムにはスプリング等の構造となり金型が大きくなる。
機械設計の知識を得て設計努力で小型化する。
3)パンチの設計
- 精密微細金型の場合、パンチが微細となるのでパンチ全長は30mm~40mmとする。
- 精密微細金型ではパンチの破損や消耗で交換する機会が多い。
金型の分解を最小限にする設計が好ましい。
事例
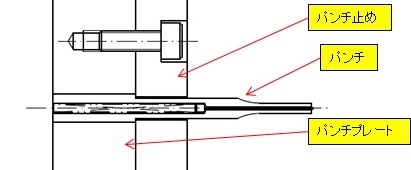
4)パイロットの設計
順送型の場合は材料を順次送って加工するので製品精度を確保する上でパイロットは重要。
パイロットはパンチプレートに植えるタイプとストリッパに固定するタイプの2種類が市販されているが、精密微細順送型ではストリッパが加工精度において最も重要なプレートなので、ストリッパに固定するパイロットを採用する。
精密微細順送型用固定パイロット
- パイロット先端径は、パイロット穴抜きパンチ径より0.005mm~0.02mm細くする。
- パイロット先端のガイド部分はラップ仕上げとする。
- 生産量の多い金型の場合は、パイロットの材質は超硬製とする。
- 材料が0.15mm以下の材料の場合、パイロット受けを設置する。
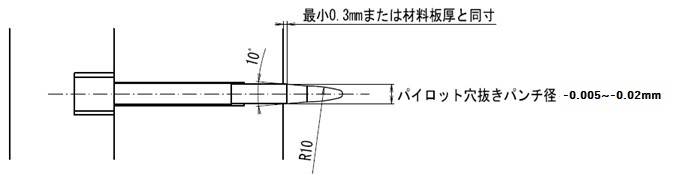
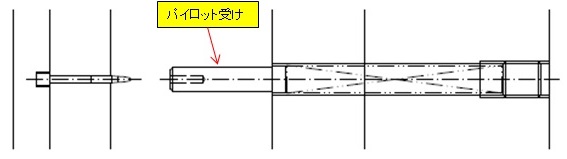
5)ダイの設計
精密微細部品で生産量が少ない金型のダイは一体構造が金型精度で有利となる。
生産量が多い場合は、ダイが摩耗でバリの発生となるので入れ駒とし交換が容易になる設計とする。
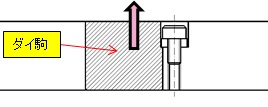
6)ストリッパの設計
精密微細部品で生産量が少ない金型のストリッパは一体構造が金型精度で有利となる。
生産量が多い場合は、ストリッパが摩耗しパンチとの隙間が大きくなり製品精度に影響するので入れ駒とし交換が容易になる設計とする。
ストリッパ入れ駒はストリッパ本体を分解せずに交換が可能な構造とする。
パンチの先端をガイドする部分は、ストリッパにパンチが入るときにパンチ先端を破損することがあるのでストリッパの裏をテーパで逃がす。
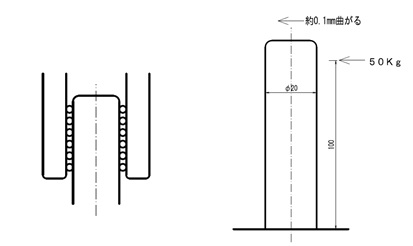
7)精密微細絞り順送型の設計
絞り順送型は、上絞りと下絞りが考えられるが、微細絞りでは下絞りが一般的。
8)抜きのカス上がり、カス詰まりの原因と対策(カス=スクラップ)
(1)抜きカス上がりの原因
微細抜きでは、抜きカスが自重でダイの下に落下することは期待できず、下記の要因でのカス上がりが考えられる。
抜きカスが油で密着する場合
抜きカスに付着した油のせいでパンチ底面に密着すると、パンチと共に上昇する場合がある
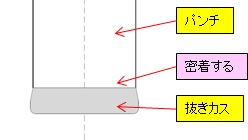
ストリッパ下面よりパンチ底面が中にある場合
パンチとストリッパのクリアランス(=隙間)が極小のため、抜き後上昇する際にストリッパ下面とパンチ底面の空間が真空となり抜きカスが上昇する。

(2)抜きカス詰まりの原因
微細抜きで特に丸形状または丸に近い形状の場合はダイまたはダイバッキング、ダイホルダーで詰まることがある。
加工油により抜きカスがプレートの側面に付着し詰まる。抜きカスが詰まるとパンチ破損の原因となる。
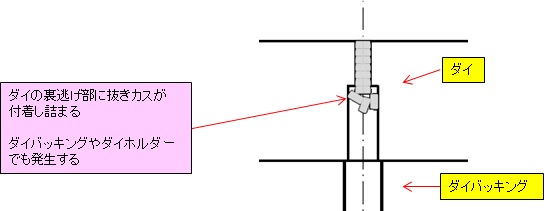
(3)抜きカス上がりの対策事例
抜きパンチにエアー穴を空け上から吹く
パンチ内部にエジェクトピンを設置する
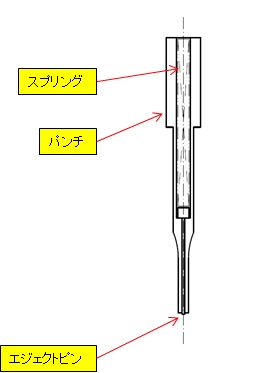
微細抜きパンチの場合
抜きパンチに穴を空けられない微細抜きパンチの場合はパンチ先端面に凹みを付けパンチと抜きカスの接触面積を少なくする
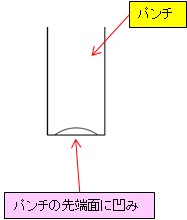
抜きパンチと抜きダイのクリアランス(=隙間)を少なく設定し抜きカスの剪断面を多くする。
抜きダイにはストレート部を設け抜きカスがダイに食いつくようにする。
※箔材抜きではダイの逃げ角は0.22°(片側)が適当。
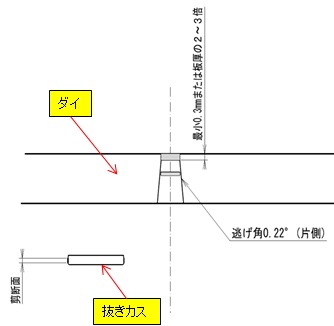
(4)抜きカス詰まりの対策事例
微細な抜きは、ダイやダイバッキング、ダイホルダーで抜きカスが詰まり抜きパンチが破損することがある。
原因
カス上がり対策と矛盾するが、ダイの切り刃のストレート部が長いとダイが摩耗した際に逆テーパとなることがあり抜きカスが詰まる。
加工油により、ダイバッキングやダイホルダーの逃げ穴の側面に付着し抜きカスが詰まる。特に、加工油が金型に付着し時間が経過すると接着剤に似た状態となる。
対策事例
下図のようにダイホルダー側面からエアーにより強制的に抜きカスを排除する。
ある程度の生産が完了したら、金型を洗浄し加工油を洗い落とす。
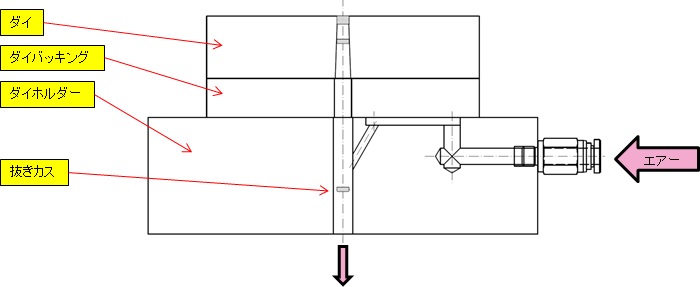
9)精密微細金型部品公差の決め方事例
I.パンチ、ダイ、ストリッパの公差の事例
材料(SUS304CSP-1/2H T=0.1mm)に対してΦ0.2mmの穴を明ける場合のパンチとストリッパとダイの寸法と公差の事例
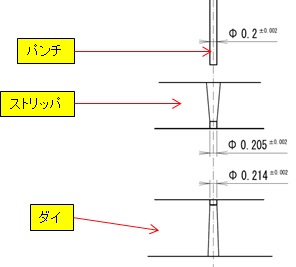
パンチ:径:Φ0.2mm / 公差:±0.002mm
ストリッパ :穴径:Φ0.205mm / 公差:±0.002mm
ダイ:穴径:Φ0.214mm / 公差:±0.002mm
II.入れ駒の公差の事例
入れ駒が生産中に動作しない場合

X:公差-0.002mm~-0.005mm
Y:公差+0.002mm~±0mm
入れ駒が生産中に動作する場合
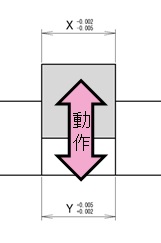
X:公差-0.002mm~-0.005mm
Y:公差+0.005mm~+0.002mm
10)金型部品の材質
I.各プレートの材質事例
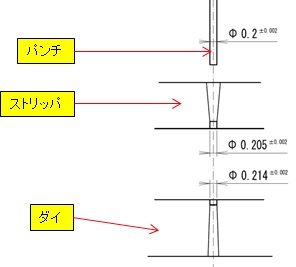
II.パンチ、ダイ駒、ストリッパ駒の材質
パンチ
微細精密部品のパンチは耐摩耗性で超硬材を使用する。
生産量が少ない場合も微細パンチは研削が困難なので超硬材を使用する。
ダイ駒
生産量が多い場合は、耐摩耗性から超硬材を使用する。
但し、ニッケルが含有しているステンレスを加工する場合は微粒子超硬を使用する。
ストリッパ駒
パンチの摩耗よりストリッパ駒の摩耗が先になるよう、SKH51 HRC61~64を使用する。
超硬の種類と粒子径
微粒子超硬粒径0.8~1.5μm
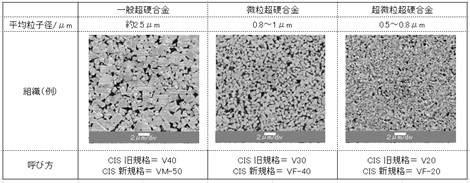
※禁・無断転用、転載